THE GREENMINE INDUSTRIAL PROCESS
After its collection, the waste is deposited by the truck in a container unit, the hopper. The hopper has a large storage capacity so the plant can run continuously with the waste gradually released according to the oven’s capacity. The waste is fed directly into the hopper in the same condition it has been collected.
No waste separation or manual input is required. The waste is fed into the carbonization oven via a conveyor belt, and is heated to 900C, beginning the recycling process.
The hopper is enclosed with strong metal gates and an exhaust system that isolates the waste smells even inside the processing unit. With no odors, problems associated with the attraction of animals such as birds, rats and flies are eliminated.
Waste carbonization means there is no oxygen inside the oven, therefore, so no burning flames and the usual toxic fumes from combustion, even at 900C. The waste is heated and dehydrated turning into char, not burnt or melted.
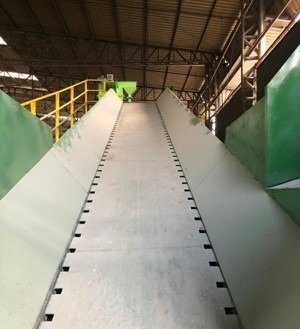
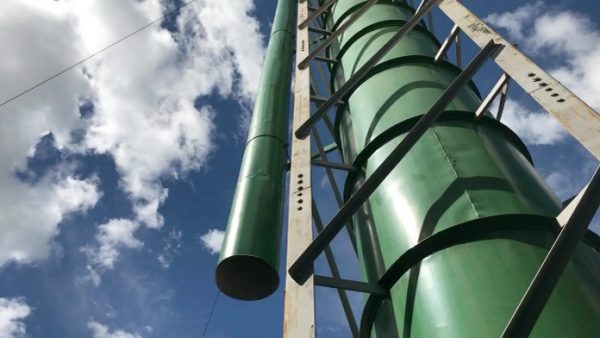
Also, alongside the waste, all leachate is collected through a gutter mounted on the underside of the hopper, and this is also fed into the oven.
A collector is located on the top side of the oven where all gases generated by the process are channeled through a tube to the distiller.
Inside the WCP all gases are retrieved, distilled, liquified and turned into a powerful highly marketable bio-liquid called pyroligneous extract.
The pyroligneous extract is a liquid substance widely used in various industrial processes as well as in farming.
The tube returning from the distiller goes to a filter where the gas temperature is reduced to minus 93C. During this step, all solid particles are retrieved and separated and only water is released to the atmosphere in vapor form.
CLIMATE CHANGE ASPECTS
Considering the causal relationship between human activity and global warming, GreenMine’s model contributes to the reduction of greenhouse gases and qualifies to obtain carbon credits by the terms of the Paris Agreement and other voluntary schemes.
GreenMine achieves this by the elimination of landfill issues and aborting methane emissions associated with decomposing organic matter, and through this addresses a cause of increasing global temperatures.
GreenMine Equipment
Some basic equipment is required to set up a GreenMine plant.
Receiving The Feedstock
The feedstock will continue to be collected by garbage collection vehicles.
A Thermal Process
GreenMine is a thermochemical decomposition of organic material.
Distiller And Recuperator
The dry and humid vapours formed in the GreenMine furnace are routed to the distiller.
Cooling Area Or Quarantine
After the GreenMine process, residues are transferred to a ‘cooling and formulation’ area.
Separation Of Materials
The automated system ‘sends a message’ indicating the lowered temperature
Formulation
This is responsible for the addition of vegetable pigments that aid in the agglomeration of the biochar.
Bio-coal Briquette Production (Optional)
The briquette machine, a component of the plant’s equipment, forms the bio-coal.
Waste And Bio-coal Production
GreenMine plants are designed to include degraded waste buried in landfill that can be mixed into the new feedstock.