THE INTRODUCTION
GreenMine’s WCPs can process existing legacy landfill waste as well as new waste producing marketable offtakes as follows:
- Mineral recyclables
- Biochar
- Bio fuel
- Rare earth elements (REE)
- Pyroligneous extract (which can be separated into tar, lignin, acidic water and bio-oils)
- Thermo-recyclables generation from bio-coal connected to the grid for distribution to communities
- Carbon credits
The technology addresses serious environmental, social and urban issues caused by toxic landfill sites and the ongoing legacy of high maintenance capped landfill sites emitting noxious gasses into the atmosphere contributing to health issues in surrounding urban areas.
Legacy landfill sites are becoming increasingly more difficult to manage and space is not readily available for future landfill sites. These sites could be better utilised for the benefit of local communities, creating a safer and healthier environment by putting the land to better use. The technology addresses the increasing need for efficient and safe disposal while transforming waste into recyclable commodities and optional clean energy.
In addition to the many benefits our technology provides in the conversion of waste, we believe our WCPs are a gamechanger as they have the potential to make landfills a thing of the past and contribute to the reduction of greenhouse gases.
THE TECHNOLOGY
There are over 500 operational landfill sites throughout the UK. There are many more capped landfill sites that still emit climate warming and noxious gases. In addition, there are circa 1,500 coastal landfill sites which are exposing waste due to coastal erosion.
According to our own proprietary GIS based landfill data software platform, we estimate there are circa 500 capped and operational landfills in the UK consistent with government data, with an average size of 500-600 acres (202-243 hectares). Many of these sites are close to towns which over time have been encroached by ever increasing urbanization, and are in close proximity to, or actually built on these legacy landfill sites often releasing noxious emissions and attracting pests which are creating health problems for the surrounding communities.
Many Landfill sites occupy land from which the legacy waste can be processed in situ and ultimately become viable real estate opportunities.
Dependent on the required speed of landfill reclamation, additional WCP modules can be utilised to increase processing capacity as required. A landfill gate fee for new waste is now circa £90.00 per tonne.
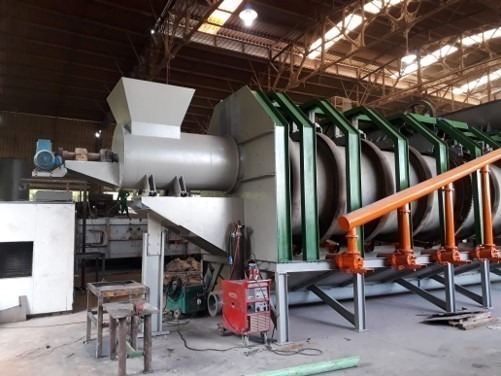
The technology uses a system that ensures the plant is 100% self-sustainable.
- It utilizes only 10% of its own produced bio-coal to heat the Pyrolysis oven. No outsourced fuel or gas are required (except for the initial ignition). Limited electricity is required to run the 40hp electric motors on start-up.
- The plant is modular in design and can be scaled up from 500kg per hour to 20 tone per hour.
- All gases from the enclosed waste carbonization process are retrieved and recuperated by a highly efficient distilling structure (using the proprietary technology of our partners).
INTERNAL LAYOUT OF EQUIPMENT
- Odor Exhaust
- Hopper
- Slurry Collector
- Conveyor Belt
- Carbonization Oven
- Gas Collector
- Coal Feeder
- Separator
- Recyclables
- Distiller
- WCP Technology
- Coal Feeder For Boiler
- Boiler
- Cooler
- Generator
- Turbine
- Odor Final Stage Water Vapor
- Electrical Substation

Innovative Technology
Our process uses innovative technology in that it prevents pollutant emissions and solid residues during processing, and in their deployment and operation.
Short Time Frame
The equipment can be built within a short time frame and installed in relatively small spaces.
Self-Sustainable
Our technology runs a system that renders the plant 100% self-sustainable: it utilizes only 10% of its own produced bio-coal to heat the carbonization oven.
Proprietary Technology
All gases from the enclosed GreenMine process are retrieved and recuperated by a highly efficient distilling structure.
BIO-PRODUCTS, RECYCLING & SUSTAINABILITY
With the waste carbonization process almost complete, much of the solid waste is now transformed into charcoal (char ashes) and other solid products.
These solid products come out of the oven separated, clean and ready for the recycling industry.
They are then sorted through a rotation metal tube according to the different types of materials contained in the GreenMine waste: aluminum, glass, iron, copper, bronze, sand and rocks.
Only 10% of the bio-coal produced from the processing will return to the oven’s furnace, which operates continuously. This means that the plant is self-sustaining producing its own bio-fuel.
The remaining 90% of the bio-coal produced can have several destinations; the majority are clean recyclables and power generation.
The bio-liquid, named pyroligneous extract, resulting from gases, is also separated and sold to many industries (construction, cosmetic and oil).
Paper & Cardboard
Food
Metal & Glass
Plastic
Wood & Garden Waste
Textile, Rubber & Leather
Others including hazardous materials
WASTE MANAGEMENT & GREENMINE
General Process
The municipal solid waste industry has had for many years four components: recycling, composting, disposal, and waste-to-energy via incineration.
Process
The conversion of an organic substance into carbon or a carbon-containing residue through destructive distillation.
Carbonization
We use extreme pyrolysis called carbonization which in its turn is a thermochemical decomposition of organic material at elevated temperatures in the absence of oxygen (or any halogen).
The Difference
The municipal solid waste processing through pyrolysise (as opposed to incineration) is one of the safest and newest alternatives methods in the world to waste management.